News Events
Latest News
Maintenance of carbide milling cutters
Release time:
Dec 22,2023
Follow the rules for tool maintenance and repair, and monitor tool wear.Good maintenance of carbide milling cutters can extend the life of the tool and improve work efficiency.
When the axis line of the carbide milling cutter and the edge line of the workpiece overlap or close to the edge line of the workpiece, the situation will be very serious, and the operator should do the related equipment maintenance work:
1. Check the power and rigidity of the machine to ensure that the required milling cutter diameter can be used on the machine.
2. The tool overhang on the spindle should be as short as possible to reduce the influence of the milling cutter axis and the position of the workpiece on the impact load.
3. Adopt the correct tooth spacing of the milling cutter for the process to ensure that there are not too many inserts engaging with the workpiece at the same time to cause vibration during cutting, and on the other hand, ensure that there are enough inserts engaging with the workpiece when milling narrow workpieces or milling cavities.
4. Ensure that a feed per insert is used so that the correct cutting results are obtained when the chips are thick enough to reduce tool wear. Use indexable inserts with a positive rake angle groove for smooth cutting and minimum power.
5. Select the milling cutter diameter appropriate to the width of the workpiece.
6. Select the correct main offset angle.
7. Place the milling cutter correctly.
8. Use cutting fluids only when necessary.
9. Follow the rules for tool maintenance and repair, and monitor tool wear.
Good maintenance of carbide milling cutters can extend the life of the tool and improve work efficiency.
:Next Page
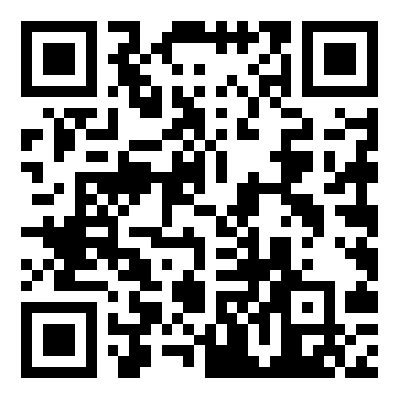
Follow Us